Key Takeaways:
- Regular cleaning and maintenance are vital for the optimal performance of CNC machines.
- Follow a comprehensive cleaning checklist and implement preventive maintenance practices.
- Proactive maintenance prevents unexpected breakdowns and extends the lifespan of your CNC machine.
- Adhere to a scheduled cleaning routine and use recommended cleaning products.
- Consider using maintenance management software like Limble CMMS for streamlined maintenance processes.
The Importance of Proactive CNC Machine Maintenance
Regular maintenance is crucial for keeping your CNC machine running smoothly and avoiding costly manufacturing downtime. Taking a proactive approach to maintenance with a well-defined preventive maintenance regimen can help ensure that your machine remains in optimal condition, resulting in improved energy efficiency and a longer useful life. By implementing a proactive maintenance routine, you can prevent unexpected breakdowns and maximize productivity. A well-maintained machine operates more efficiently, reducing energy consumption and minimizing the risk of malfunctions or errors. This not only saves you money on electricity bills but also extends the lifespan of your CNC machine, reducing the need for costly repairs or replacements. Additionally, a well-maintained machine can help you meet production deadlines and customer demands. By addressing potential issues before they escalate, you can minimize manufacturing downtime and keep your operations running smoothly. Investing time and resources into proactive CNC machine maintenance is a wise decision that will pay off in the long run.
Quote:
“Regular maintenance is like giving your CNC machine a check-up. It ensures that everything is in working order and helps prevent major issues down the line.” – CNC Machine Expert
Common CNC Maintenance Challenges
Maintaining CNC machines involves addressing various challenges related to mechanical components, electrical equipment, electronics components, and software. These challenges can impact the performance, efficiency, and longevity of the machines. Understanding and overcoming these common challenges is essential for effective CNC machine maintenance.Time Constraints
One of the primary challenges in CNC machine maintenance is time constraints. CNC machines play a critical role in the manufacturing process, and any downtime can result in significant production loss. This limits the time available for maintenance tasks. Technicians and operators need to efficiently manage their time to ensure routine maintenance is carried out while minimizing disruptions to production schedules.Excessive Machine Vibration
Excessive machine vibration is another common challenge in CNC machine maintenance. Vibrations can affect the precision and accuracy of machining operations, leading to compromised product quality. Identifying the root causes of vibration, such as incorrectly aligned components or worn-out parts, and implementing appropriate corrective measures is crucial for maintaining optimal machine performance.Overheating
Overheating is a significant concern in CNC machine maintenance. Increased workload, coolant issues, or inadequate cooling systems can lead to overheating, which can result in reduced machine performance and potential damage to critical components. Regular monitoring of coolant levels, coolant circulation, and cooling fans is necessary to prevent overheating and ensure stable machine operation.Software Issues
Software issues pose a unique challenge in CNC machine maintenance. CNC machines rely on software programs to execute machining operations accurately. However, software glitches, compatibility issues, or outdated programs can cause delays, errors, or even machine malfunctions. Keeping software up to date and performing regular checks and updates is essential to maintain optimal machine performance.Power Supply Issues
Power supply issues can also affect CNC machine maintenance. Fluctuations in power supply voltage, inadequate grounding, or power surges can damage electrical components and disrupt machine operations. Implementing effective power supply protection measures, such as voltage stabilizers and surge suppressors, can help prevent power-related issues and ensure consistent machine performance.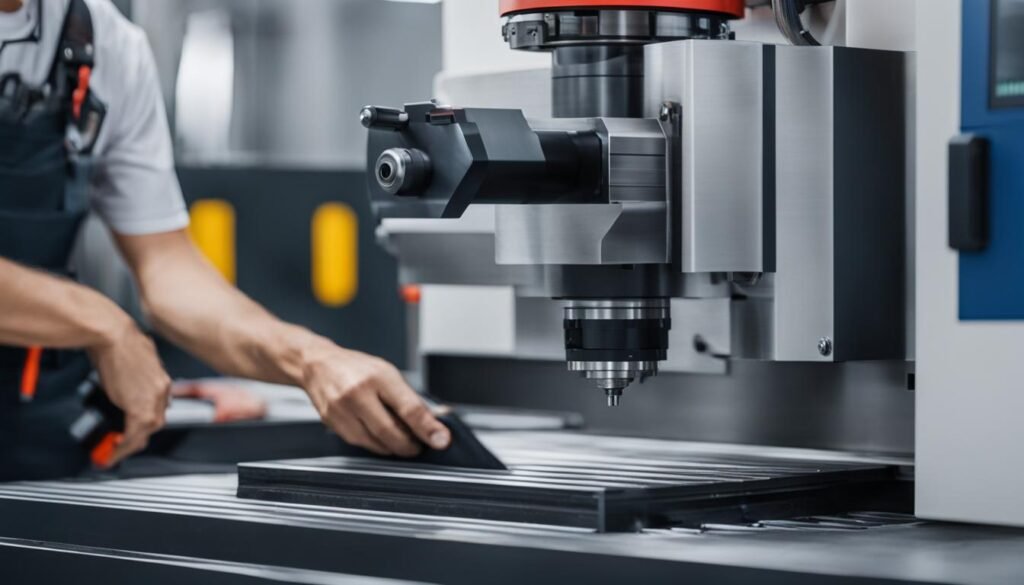
Tips and Best Practices for CNC Machine Maintenance
Proper maintenance is key to ensuring the longevity and optimal performance of your CNC machine. By following these tips and best practices, you can keep your machine running smoothly and prevent unexpected breakdowns.Maintain Thorough Maintenance Records
Keeping detailed records of all maintenance activities is essential. This will help you track the history of your machine’s maintenance, identify recurring issues, and plan for future maintenance tasks. Thorough records also play a crucial role in warranty claims and can help you demonstrate compliance with manufacturer recommendations.Provide Adequate Employee Training
Well-trained employees are essential for effective CNC machine maintenance. Make sure that your technicians and operators receive proper training on machine maintenance procedures, safety protocols, and troubleshooting techniques. Regular training sessions should be conducted to keep employees up to date with the latest maintenance practices and technologies.Maintain a Clean Machine Environment
A clean machine environment is vital for preventing debris, dust, and contaminants from interfering with your machine’s performance. Regularly clean the machine and its surrounding area to remove dirt and debris. Pay special attention to the machine’s cooling system to ensure proper airflow and prevent overheating.Monitor Machine Operations and Implement Regular Breaks
Regularly monitor your machine’s operations for any performance anomalies or signs of wear and tear. Implementing regular breaks in machine operation can help prevent overheating and relieve stress on the machine components. This practice can significantly extend the lifespan of your machine and improve its overall performance.Establish Standard Operating Procedures and Use Maintenance Checklists
Standard operating procedures (SOPs) provide clear instructions for routine maintenance tasks and help maintain consistency across maintenance activities. Develop SOPs specific to your machine and ensure that all technicians and operators follow them. Additionally, use maintenance checklists to ensure that all necessary maintenance tasks are performed and documented properly.
CNC Machine Maintenance Checklists
Maintenance checklists are essential tools for ensuring the proper upkeep and performance of CNC machines. By following these checklists at regular intervals, you can identify potential issues early on, address them promptly, and prevent costly breakdowns. Here, we provide you with comprehensive checklists for daily, weekly, monthly, and annual maintenance tasks to help you keep your CNC machines operating smoothly.Daily Maintenance Checklist
Performing daily maintenance tasks is crucial for maintaining the optimal performance of your CNC machine. Here are some important tasks to include in your daily checklist:- Inspect the pressure and level of lubricant to ensure proper lubrication.
- Check the coolant level and top up if necessary.
- Clean the coolant disposal tray to prevent buildup.
- Check for the presence of moisture in the pneumatic air system and adjust the pressure if needed.
- Wipe down machine surfaces to remove any debris or contaminants.
- Check the output of the voltage stabilizer and the temperature of the panel cooler.
- Observe the machine operation for any anomalies or unusual sounds.
Weekly Maintenance Checklist
In addition to daily maintenance, it is important to perform weekly maintenance tasks to address any potential issues that may arise. Here are some tasks to include in your weekly checklist:- Clean the machine shop to maintain a clean working environment.
- Check for any oil or coolant leakage and address it promptly.
- Ensure that the cooling fans are functioning properly to prevent overheating.
- Perform a visual inspection of machine components for any signs of wear or damage.
- Check the tool heads in the tool changer and ensure their proper functioning.
- Lubricate machine parts as specified in the manufacturer’s guidelines.
- Inspect and maintain pneumatic pumps and chucks to ensure their reliability.
Monthly Maintenance Checklist
Monthly maintenance tasks are essential for keeping your CNC machine in optimal condition. Here are some tasks to include in your monthly checklist:- Clean the chip collector to prevent clogs and maintain proper airflow.
- Inspect and adjust jaws and fixtures to ensure accurate machining.
- Clean or replace air filters to maintain proper air quality.
- Check the condition of tool heads and replace any damaged or worn-out tools.
- Inspect and maintain chains and conveyors to ensure smooth operation.
- Clean the machine fans to prevent overheating.
- Inspect oil and coolant logs and top up or replace fluids as necessary.
- Clean radiator grills to maintain proper cooling.
Annual Maintenance Checklist
Annual maintenance tasks are critical for the long-term performance and reliability of your CNC machine. Here are some tasks to include in your annual checklist:- Inspect the coolant tank for any signs of contamination or deterioration.
- Clean the coolant cylinder to remove any buildup.
- Drain and refill the lubricant to ensure optimal lubrication.
- Inspect the pneumatic oil and replace it if necessary.
- Replace the oil filters to maintain proper filtration.
- Check software alignment and update as needed.
- Inspect the electrical supply and address any issues promptly.
- Run machine diagnostics to check for any potential problems.
Daily Maintenance Checklist
Proper daily maintenance is essential to ensure the optimal performance and longevity of your CNC machine. By incorporating these tasks into your daily routine, you can prevent unnecessary breakdowns and keep your machine running smoothly. Here is a comprehensive checklist of daily maintenance tasks:- Inspect the pressure and level of lubricant to ensure proper lubrication of moving parts.
- Check the coolant level and top up if necessary to maintain the appropriate cooling and lubrication.
- Clean the coolant disposal tray to prevent clogs and maintain system efficiency.
- Check for moisture in the pneumatic air and remove any excess moisture to prevent damage to sensitive pneumatic components.
- Check the pressure of the pneumatic air to ensure optimal machine operation.
- Wipe machine surfaces to remove any debris or dust that could affect performance or accuracy.
- Check the voltage stabilizer output to ensure a stable power supply.
- Monitor the panel cooler temperature to prevent overheating and ensure proper machine cooling.
- Observe machine operation for any anomalies, such as unusual sounds or vibrations, and address them promptly.
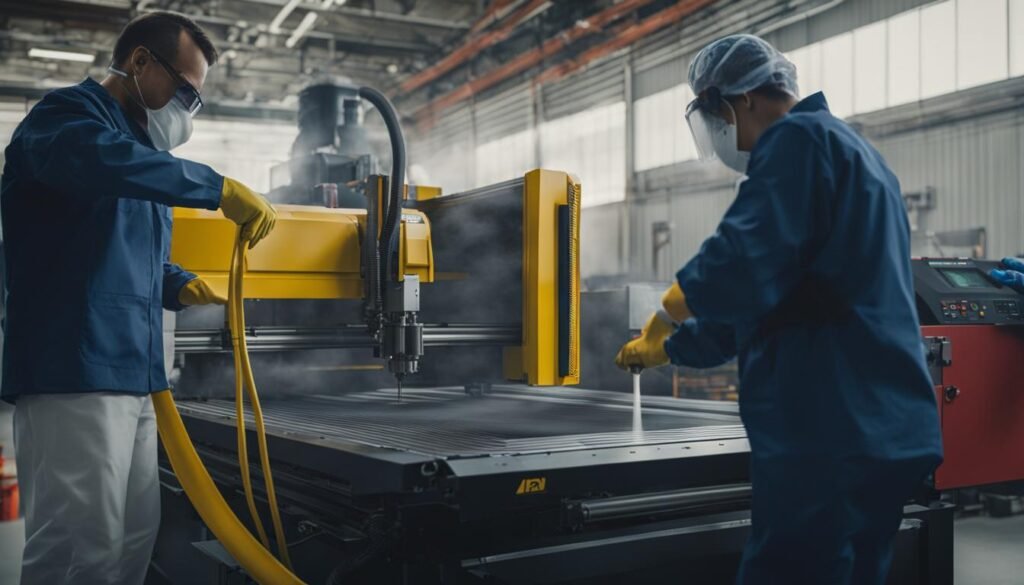
Weekly Maintenance Checklist
Regular weekly maintenance is crucial for keeping your CNC machine running smoothly and preventing costly breakdowns. By following this checklist, you can ensure that your machine shop remains clean, components are inspected, and necessary lubrication is applied. Let’s go through the essential tasks you need to perform on a weekly basis:Table: Weekly Maintenance Checklist
Task | Description |
---|---|
Clean Machine Shop | Remove debris and dust from the machine shop area to maintain a clean working environment. |
Check for Oil and Coolant Leakage | Inspect the machine for any signs of oil or coolant leakage. Address any leaks promptly to prevent damage to the machine or other components. |
Ensure Cooling Fans Are Working Properly | Check the cooling fans to ensure they are operating effectively. Overheating can lead to premature wear and tear of machine components. |
Perform Visual Inspection of Machine Components | Visually inspect all machine components for any signs of damage, wear, or misalignment. Address any issues immediately to prevent further damage. |
Check Tool Heads in Tool Changer | Verify that the tool heads in the tool changer are secure and properly aligned. This helps ensure accurate machining and prevents accidents. |
Lubricate Machine Parts | Apply lubricant to the designated areas to reduce friction and maintain smooth operation of moving parts. Refer to the machine’s manual for the appropriate lubricant. |
Check Pneumatic Pumps and Chucks | Inspect pneumatic pumps and chucks for any leaks or irregularities. Proper pneumatic system function is crucial for tool clamping and release. |

The Monthly Maintenance Checklist for CNC Machines
Regular monthly maintenance is crucial to ensure the optimal performance and longevity of your CNC machines. By following a comprehensive monthly maintenance checklist, you can address potential issues and keep your machines running smoothly. Here are the essential tasks to include in your monthly maintenance routine:Inspect and adjust jaws and fixtures
Check the jaws and fixtures of your CNC machine and ensure they are properly aligned and functioning correctly. Any misalignment can result in inaccurate machining and decreased productivity. Make any necessary adjustments to maintain precision and reliability.Clean or replace air filters
Inspect the air filters of your CNC machine and clean or replace them as needed. Clogged or dirty air filters can restrict airflow and lead to overheating, reduced performance, and potential damage to the machine. Regularly maintaining clean air filters ensures the efficient operation of your CNC equipment.Check the condition of tool heads
Inspect the condition of the tool heads on your CNC machine. Look for any signs of wear, damage, or misalignment. Properly functioning tool heads are crucial for accurate machining and the production of high-quality parts. Replace or repair any damaged tool heads to maintain optimal performance.Inspect and maintain chains and conveyors
Examine the chains and conveyors of your CNC machine for any signs of wear, malfunctions, or buildup of debris. Clean and lubricate these components as necessary to ensure smooth operation. Regular maintenance of chains and conveyors prevents unexpected failures and prolongs the life of your machine.Clean machine fans
Remove any dust, debris, or buildup from the machine fans. Clean fans contribute to proper machine ventilation and prevent overheating. Ensure that the fans are functioning efficiently and replace any faulty fans promptly.Inspect oil and coolant logs
Check the oil and coolant logs of your CNC machine to ensure they are at the appropriate levels. Regularly monitor the condition of the oils and coolants to detect any signs of contamination or deterioration. Maintain proper levels and quality of lubricants and coolant for optimal machine performance and longevity.Clean radiator grills
Thoroughly clean the radiator grills of your CNC machine to remove any dirt, debris, or obstructions. Clear radiator grills enable proper heat dissipation and prevent overheating. Regular cleaning of radiator grills is essential for maintaining optimal machine temperature and performance. By diligently following this monthly maintenance checklist, you can prevent potential issues, reduce downtime, and extend the lifespan of your CNC machines. Incorporate these tasks into your regular maintenance schedule to ensure the continued reliability and productivity of your equipment.
Annual Maintenance Checklist
Regular annual maintenance is crucial for ensuring the longevity and optimal performance of your CNC machine. By following this checklist, you can identify and address any potential issues, keeping your machine running smoothly throughout the year.Inspect Coolant Tank
Start by inspecting the coolant tank for any signs of contamination or damage. Check for debris, sludge, or metal shavings that may have accumulated over time. If necessary, clean the tank and replace the coolant to maintain efficient cooling and prevent damage to the machine.Clean Coolant Cylinder
The coolant cylinder plays a vital role in regulating the temperature of your CNC machine. Clean the cylinder thoroughly, removing any built-up residue or contaminants that could affect its performance. Regular cleaning will ensure proper coolant flow and prevent overheating.Drain and Refill Lubricant
Lubrication is essential for smooth machine operation and to prevent wear and tear on moving parts. Drain and replace the lubricant according to the manufacturer’s guidelines, taking care to use the recommended type and quantity. Regular lubricant changes will help maintain optimal machine performance and extend its lifespan.Inspect Pneumatic Oil
The pneumatic system plays a crucial role in many CNC machines. Inspect the pneumatic oil reservoir and check for adequate oil levels. If the oil appears dirty or contaminated, it may be necessary to drain and replace it. Proper pneumatic oil maintenance will help prevent issues such as air leaks and suboptimal machine performance.Replace Oil Filters
Oil filters help remove impurities from the lubricant, ensuring that it remains clean and free from contaminants. Replace the oil filters as recommended by the manufacturer to maintain the quality of the lubricant and prevent potential damage to the machine.Check Software Alignment
Verify the alignment of the software used to control the CNC machine. Ensure that all software components are up to date and properly aligned to avoid any compatibility issues or programming errors that may affect the machine’s performance.Check Electrical Supply
Inspect the electrical supply and connections to ensure that there are no loose wires, frayed cables, or other electrical issues. Test the electrical supply to confirm that the machine is receiving the proper voltage and that there are no fluctuations or interruptions that could disrupt its operation.Run Machine Diagnostics
Perform comprehensive machine diagnostics to identify any underlying issues or potential areas of concern. Run diagnostic tests provided by the manufacturer or use specialized diagnostic software to assess the overall health and performance of your CNC machine. Address any identified issues promptly to avoid potential breakdowns or production delays. By following this annual maintenance checklist, you can ensure that your CNC machine remains in top condition throughout the year. Remember to consult the manufacturer’s guidelines and recommendations specific to your machine model for detailed instructions and additional maintenance tasks.Importance of Regular Maintenance Scheduling
Regular maintenance scheduling plays a crucial role in keeping your CNC machines operating at their optimum level. By implementing a proactive maintenance plan, you can ensure machine uptime, increase equipment lifespan, achieve cost savings, improve productivity, reduce downtime, and optimize overall performance. One of the key benefits of regular maintenance scheduling is machine uptime. By regularly inspecting and maintaining your CNC machines, you can prevent unexpected breakdowns and minimize unplanned downtime. This allows for uninterrupted production and ensures that your machines are consistently available when you need them. Moreover, regular maintenance scheduling significantly contributes to extending the lifespan of your CNC equipment. By identifying and addressing potential issues early on, you can prevent major breakdowns and costly repairs. This approach helps to maximize the useful life of your machines, saving you money in the long run. Another advantage of regular maintenance is improved productivity. When your CNC machines are properly maintained, they operate more efficiently, leading to increased production output. Routine inspections, lubrication, and cleaning ensure that all components are functioning optimally, resulting in higher accuracy, reduced errors, and improved overall performance. Additionally, regular maintenance scheduling offers the opportunity to optimize machine performance. Through regular inspections and adjustments, you can identify and correct any issues that may be affecting the quality of your output. This proactive approach allows you to fine-tune your machines, ensuring that they consistently deliver the desired results. In summary, regular maintenance scheduling is essential for maintaining machine uptime, extending equipment lifespan, achieving cost savings, improving productivity, reducing downtime, and optimizing overall performance. By implementing a comprehensive maintenance plan and adhering to a regular schedule, you can ensure that your CNC machines operate at their full potential, ultimately benefiting your business in numerous ways.Your Comprehensive CNC Machine Maintenance Guide
Proper maintenance of CNC machines is crucial for ensuring their longevity and maximizing productivity. By following a comprehensive cleaning checklist and implementing preventive maintenance practices, you can extend the lifespan of your CNC machines, avoid unexpected breakdowns, and reduce repair costs. Here are some key tips to keep your CNC machine in top condition:1. Regular Cleaning and Lubrication
Regularly clean all machine surfaces and components using recommended cleaning products. Remove chips, debris, and coolant residues to prevent them from affecting machine performance. Additionally, ensure proper lubrication of mechanical parts to reduce friction and prevent premature wear.2. Inspection and Calibration
Perform routine inspections to identify potential issues such as loose connections, worn-out belts, or misaligned components. Regularly calibrate the machine to maintain accuracy and precision. Use calibration tools and follow manufacturer guidelines for optimal results.3. Check and Monitor Coolant System
Inspect the coolant system regularly to ensure proper flow, coolant level, and quality. Clean or replace filters as needed and monitor coolant pH levels. Contaminated coolant can cause damage to machine components, so it’s essential to maintain a clean and well-maintained coolant system.4. Create a Maintenance Schedule
Establish a maintenance schedule based on the manufacturer’s recommendations and the specific needs of your CNC machine. Include daily, weekly, monthly, and annual maintenance tasks in your schedule. Use checklists and record maintenance activities to track progress and ensure all necessary tasks are completed.5. Train Machine Operators
Provide comprehensive training to machine operators on proper machine operation and maintenance procedures. Educate them about the importance of regular maintenance, cleaning practices, and safety protocols. Well-trained operators can help identify potential issues early on and contribute to the overall maintenance efforts. By following these best practices and implementing a proactive CNC machine maintenance routine, you can significantly increase the lifespan of your equipment, optimize its performance, and minimize downtime. Regular maintenance and cleaning will ensure that your CNC machine operates at its best, leading to increased productivity and improved overall efficiency.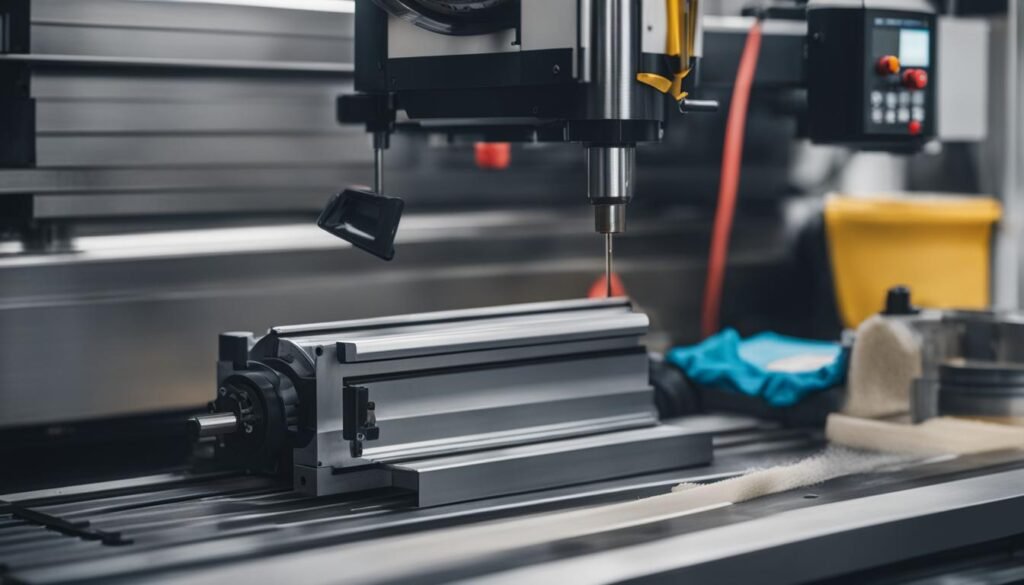
Request a Demo Today
To simplify and streamline your CNC machine maintenance, consider using maintenance management software like Limble CMMS. This powerful cloud-based software is designed specifically for managing and optimizing maintenance processes. Limble CMMS automates data collection, providing you with quick and easy access to maintenance history. You can schedule preventive maintenance work, manage spare parts inventory, and track real-time machine condition – all from one centralized platform. By implementing Limble CMMS, you can ensure that your CNC machines are maintained according to the best practices of preventive maintenance. This software keeps a record of all maintenance activities, allowing you to track and analyze machine performance over time. With Limble CMMS, you can proactively identify potential issues and take corrective action before they turn into costly breakdowns. Request a demo today and discover how Limble CMMS can improve your maintenance processes, extend the lifespan of your CNC machines, and increase productivity in your manufacturing facility. Take the first step towards efficient and effective CNC machine maintenance with Limble CMMS.FAQ
Why is proactive CNC machine maintenance important?
Proactive CNC machine maintenance is important to prevent unexpected machine failures, reduce production downtime, and ensure optimal machine performance. It also results in higher energy efficiency, longer machine lifespan, and improved product quality.
What are some common CNC maintenance challenges?
Some common CNC maintenance challenges include time constraints due to the critical role of the machines in the manufacturing process, excessive machine vibration affecting precision, overheating due to increased workload or coolant issues, software issues affecting machine output, and power supply issues causing defects in the output.
What are the best tips and practices for CNC machine maintenance?
Some best tips and practices for CNC machine maintenance include maintaining thorough maintenance records, providing adequate employee training, maintaining a clean machine environment, monitoring machine operations for anomalies, scheduling regular breaks to prevent overheating, establishing standard operating procedures, and using maintenance checklists to ensure proper machine operation and maintenance.
What are the different maintenance checklists for CNC machines?
Different maintenance checklists for CNC machines include daily, weekly, monthly, and annual maintenance checklists. These checklists help technicians and operators perform necessary maintenance tasks at different intervals to ensure the machine’s optimal performance and longevity.
What are some tasks included in the daily maintenance checklist for CNC machines?
Some tasks included in the daily maintenance checklist for CNC machines are inspecting the pressure and level of lubricant, checking the coolant level, cleaning the coolant disposal tray, checking for moisture and pressure in pneumatic air, wiping machine surfaces, checking the output of voltage stabilizer and panel cooler temperature, and observing machine operation for any anomalies.
What tasks are included in the weekly maintenance checklist for CNC machines?
Some tasks included in the weekly maintenance checklist for CNC machines are cleaning the machine shop, checking for oil and coolant leakage, ensuring proper functioning of cooling fans, performing visual inspections of machine components, checking tool heads in the tool changer, lubricating machine parts, and inspecting and maintaining pneumatic pumps and chucks.
What tasks are included in the monthly maintenance checklist for CNC machines?
Some tasks included in the monthly maintenance checklist for CNC machines are cleaning the chip collector, inspecting and adjusting jaws and fixtures, cleaning or replacing air filters, checking the condition of tool heads, inspecting and maintaining chains and conveyors, cleaning machine fans, inspecting oil and coolant logs, and cleaning radiator grills.
What tasks are included in the annual maintenance checklist for CNC machines?
Some tasks included in the annual maintenance checklist for CNC machines are inspecting the coolant tank, cleaning the coolant cylinder, draining and refilling lubricant, inspecting pneumatic oil, replacing oil filters, checking software alignment, inspecting electrical supply, and running machine diagnostics to ensure proper alignment and performance.
Why is regular maintenance scheduling important for CNC machines?
Regular maintenance scheduling is important for CNC machines to ensure machine uptime, increase equipment lifespan, reduce repair costs, improve productivity, minimize downtime, and optimize machine performance. Adhering to a regular maintenance schedule helps prevent unexpected breakdowns, maximize productivity, and achieve cost savings in the long run.
How can maintenance management software like Limble CMMS help with CNC machine maintenance?
Maintenance management software like Limble CMMS can simplify and streamline CNC machine maintenance by automating data collection, providing quick and easy access to maintenance history, helping with scheduling preventive work, managing spare parts inventory, and allowing real-time tracking of machine condition. Request a demo today to see how Limble CMMS can improve your maintenance processes.
What Are the Benefits of Precision Machining in CNC Machines?
Precision machining benefits explained: Precision machining in CNC machines offers numerous advantages. Firstly, it ensures high accuracy, allowing for the production of intricate and complex parts with tight tolerances. Secondly, it offers increased efficiency, resulting in faster production times and reduced costs. Lastly, precision machining enhances product quality and consistency, leading to improved customer satisfaction.